Customer overview
For 65 years, Vitafoam has been manufacturing a range of comfort foam products from its site in Middleton near Manchester. Formerly two cotton mills, the site close to the River Irk houses the production line and raw ingredients that are combined to make the foam. This includes hazardous chemicals that are delivered daily and held in bulk tankers, raising the potential for spills and presenting the challenge of dealing with materials and an end-product that have a high potential fire risk.
Project background
Robin Parry, the group’s Operational Excellence Engineer, is tasked with mitigating the potential for harm to people and the environment by managing spill risks on site and ensuring any possible fire water run-off would be contained. Regular maintenance alerted Robin to the fact that the site’s incumbent pneumatic closures system required replacing and Darcy was called upon to bring everything fully up to date.
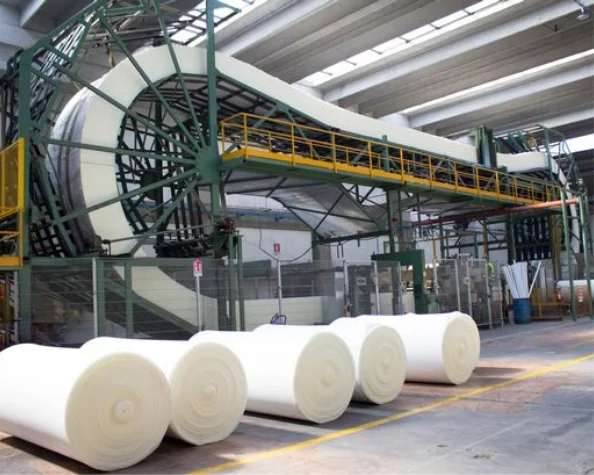
Our solution
Darcy technicians undertook a full assessment of the site, reviewing drainage surveys and detailing manhole requirements to create a tailored proposal that outlined the precise range of measures needed to guarantee containment. The busy site accommodates up to 60 lorries a day and separate third-party contracting teams were present during the project’s implementation phase, meaning the replacement system had to be introduced with speed, flexibility and minimum disruption. An annual servicing agreement now also provides Vitafoam with the peace of mind that the system’s integrity will be maintained on an ongoing basis.
Benefits
With a completely new hydraulic drain closure system and a site-wide approach to spillcare, Vitafoam’s has enforced a range of measures to protect those on site as well as the wider environment. Drain closures are integrated into the fire alarm system as an additional safeguard, activated automatically rather than relying on manual intervention. Text message alerts have also been introduced to highlight where there are any anomalies present in the system. For spills, cabinets are stocked and strategically placed, with consideration given to ease of ongoing maintenance at a site where space is at a premium. Following the successful completion of this project at Middleton, potential solutions are also being explored by Darcy for other sites across the wider Vita Group.
Robin Parry, Operational Excellence Engineer, The Vita Group: “Darcy had an open, honest and collaborative approach. They had a good grasp of what we wanted, the knowledge of the installation team was excellent, and the challenging work was completed safely, with limited interruption to other business functions. We now have a containment system that we know we can rely on in the event of a major spillage or release of firewater.”
For more information on fire-water containment solutions, including options to finance the systems, contact our team on 01732 762338 or by email.